Introduction
Every year, a significant number of warehouse injuries and more than several deaths are reported to governing bodies. The vast majority of these accidents occur as a result of the poor handling of loads and equipment. Fortunately, such incidents are entirely preventable if all employees are properly trained to recognize potential risks and avoid them.Potential Hazards
The most frequent risks when handling loads in a warehouse include:
Musculoskeletal Disorders.
Over long periods of time, improper manual lifting techniques can lead to a variety of musculoskeletal disorders, and particularly to back-related syndromes. To avoid such hazards, warehouse employees must regularly receive safety training with regard to appropriate manual and mechanical lifting techniques.Slips and falls.
Although warehousing floors must be free of cords, liquids, and virtually any other potentially dangerous items at all times, this isn’t always the case. Having to navigate obstacles is all the more difficult when manual lifting and/or mechanical carrying is involved, which is why it is necessary for workers to be constantly aware of the risk to slip and fall. Personal protective equipment can go a long way towards preventing these accidents.Forklift Accidents.
Some of the most serious incidents when handling loads in a warehouse involve forklifts. For all the benefits they provide for businesses, these machineries can cause serious damage and even death if operated improperly. Training all personnel to operate forklifts may be time-consuming, but it is vital since these vehicles are the leading cause of warehouse deaths worldwide.Hot Equipment.
When working around vehicles, conveyor belts, or other energized equipment, having the necessary Lock Out/Tag Out knowledge can help employees avoid grave incidents, such as electrocution or being caught between moving parts.
Incident Prevention
An untrained workforce that is unaware of possible hazards when handling loads in a warehouse can lead to an increased number of accidents. Employers are therefore legally required to provide the people they hire with sufficient safety training courses in order to account for the entire range of occupational risks.
A warehousing job may seem relatively straightforward in theory, but peak ordering hours can put additional pressure on workers. When employees are forced to repeatedly traverse the building to maintain their quota, accidents can easily happen. As injury and time lost claims show every year, such events continue to take place despite rising safety standards.
Given the incredibly high loads of fully stacked pallets, as well as the numerous ways in which forklifts or other electrically powered equipment can injure workers, it is vital for the latter to receive enough training for them to acknowledge the full extent of their occupational risks and have a firm grasp of the ways in which these hazards can be avoided. (need some actual measures, like correct use and maintenance of PPE for ex).
Recommended Safety Courses
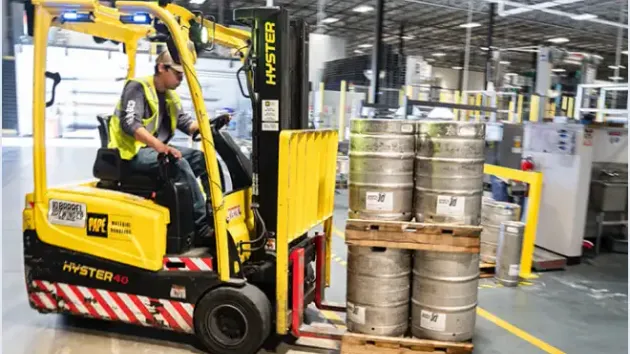
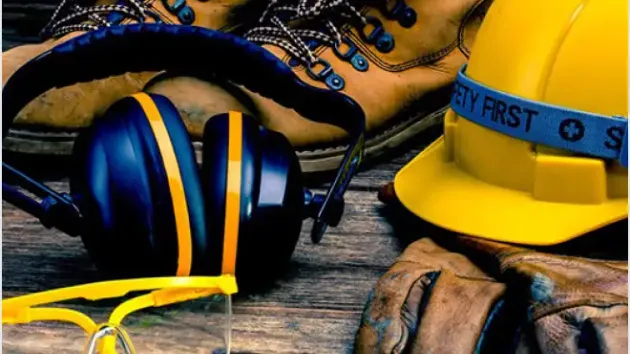
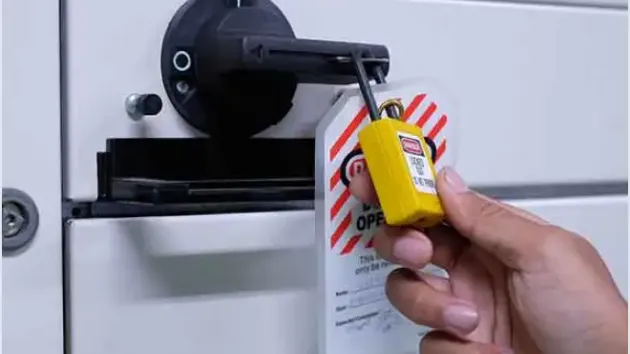
What You Can Do to Stay Safe
Whether you’re a warehouse worker, vehicle operator, or warehouse manager, the importance of safety courses cannot be overstated. Across all jurisdictions in Canada, it is the legal responsibility of the employer to ensure that all workers undergo the necessary training to maintain their safety and that of their colleagues.
To consult a complete list of safety courses that may be required in your line of work, please visit our Logistics industry page and select your occupation from the list.